PLANO, TX, Feb 28, 2024 – Siemens Digital Industries Software announced that Lazer Sport NV, one of Europe’s leading cycling helmet manufacturers, adopted the Siemens Xcelerator portfolio of industry software – to help bring KinetiCore, Lazer Sport’s new proprietary rotational impact protection technology, to market.
“At Lazer Sport, we have led bicycle helmet innovation since 1919. From simple leather caps on Belgian roads to our sleek, safe, and globally available helmets today. We are blending passion and performance for the joy of riding. Our drive for innovation redefines helmet protection with KinetiCore technology. With KinetiCore already implemented in 20 models by the end of 2024, these helmets offer enhanced safety and design for all cyclists. Our focus is on top performance, eco-friendly materials, and self-sufficient production. As we continue to grow in more markets and product categories, safety remains our priority. In the meantime, our commitment to sustainability aligns with the bike industry’s evolving needs. At the heart of our development and innovation process is Siemens Xcelerator,” said Bastiaan Van Asch, product engineering, Lazer Sport NV.
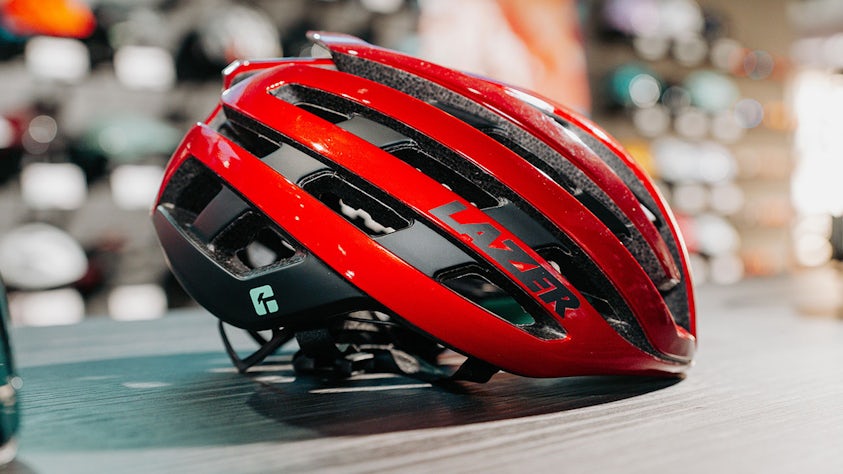
Lazer Sport NV, one of Europe’s leading cycling helmet manufacturers, adopted the Siemens Xcelerator portfolio of industry software – to help bring KinetiCore, Lazer Sport’s new proprietary rotational impact protection technology, to market.(Image credit: Lazer Sport NV)
KinetiCore is the result of Lazer Sport’s decade-long search for new and improved technology. Lazer Sport created KinetiCore to provide on- and off-road cyclists protection against both direct and rotational impact. The uniquely designed EPS foam blocks, called controlled crumple zones, deform under impact and absorb the energy that otherwise would reach the cyclist’s brain. The KinetiCore technology offers up to 23% lighter helmets, as well as 12% better cooling efficiency with innovative vents channeling cool air through to the back of the helmet and expelling warm air, boosting rider comfort and overall experience. KinetiCore is made with less plastic than previous comparable models, supporting Lazer Sport’s commitment to reducing impact on the environment.
Lazer Sport uses Siemens’ NX software for product engineering and manufacturing, along with Simcenter 3D software for digital simulation and verification. “The development of KinetiCore required a huge amount of design changes and simulations. We chose the Siemens Xcelerator portfolio for its wide range of applications and the ability to seamlessly connect 3D design with 3D printing for prototyping and digital simulation. With Siemens’ NX we were able to create more complex designs for our helmets and molds and simulate them. This allowed for greater design complexity, enhanced freedom, and faster time to market,” said Emiel Spreeuwers, product designer, Lazer Sport.
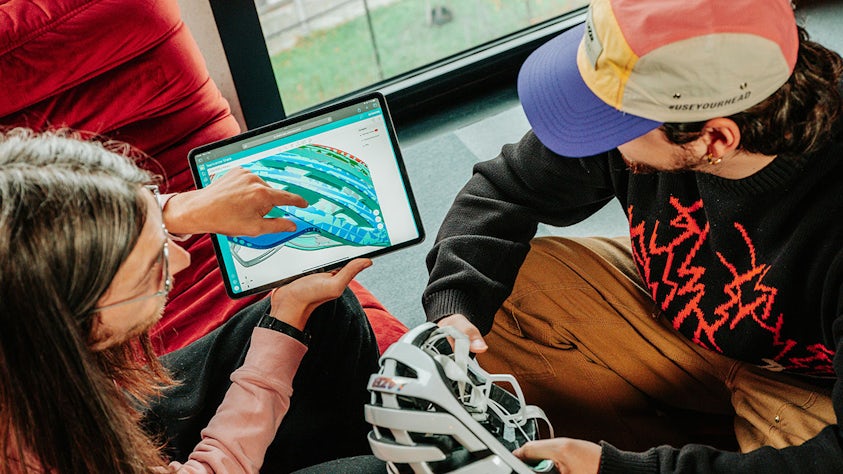
Lazer Sport is also using the Teamcenter Share app to optimize collaboration both internally and with suppliers. Delivered as a cloud service, Teamcenter Share is a controlled, secure and easy-to-access environment, enabling Lazer Sport to easily share design and engineering data. (Image credit: Lazer Sport NV)
“The 3D CAD files created in NX can also be easily opened in Simcenter for further modification and meshing without any compatibility issues. This streamlined approach helps us to verify KinetiCore’s performance, preventing costly mold modifications post-production,” said Hadi Ghiaballoo, product engineer, Lazer Sport.
Lazer Sport is also using the Teamcenter Share app, delivered as part of the Siemens Xcelerator as a Service portfolio, to optimize collaboration both internally and with suppliers. Delivered as a cloud service, Teamcenter Share is a controlled, secure and easy-to-access environment, enabling Lazer Sport to easily share design and engineering data.
To learn more about how the Siemens Xcelerator portfolio of industry software is helping pioneers and innovators in all industries, visit https://www.sw.siemens.com/en-US/digital-transformation/cloud/.
About Siemens Digital Industries Software
Siemens Digital Industries Software helps organizations of all sizes digitally transform using software, hardware and services from the Siemens Xcelerator business platform. Siemens’ software and the comprehensive digital twin enable companies to optimize their design, engineering and manufacturing processes to turn today’s ideas into the sustainable products of the future. From chips to entire systems, from product to process, across all industries. Siemens Digital Industries Software – accelerating transformation.